13
Sep
Knowing the difference between EPR and TR-XLP cables can be tricky
Share:
XLP
Cross-linked polyethylene (XLP) compound was invented during the 1950s and gained popularity during the 1960s because it provided physical protection and flexibility, making it a staple in providing improved reliability in the electrical system. Cross-linked insulation was also affordable and could be mass produced by many suppliers. Therefore, it was the right compound at the right time.
TR-XLP
Since the mid-1980s, TR-XLP has become the dominant insulation in utility distribution cable applications primarily due to lower first-cost and lower operating losses. TR-XLP compound continues to be improved and is provided by many cable manufacturers in the United States and the rest of the world.
TRXLPE compounds are rated 90ºC for normal operation, 130ºC for emergency operation and 250ºC short circuit.
EPR
The first versions of EPR (ethylene propylene rubber-insulated), introduced in the early 1960s, demonstrated favorable characteristics that were quickly recognized by cable manufacturers. It presented weathering stability, heat resistance up to 160ºC, low temperature flexibility, and it was easily extruded.
Over the years, EPR insulation has become the standard insulation for most industrial applications, and in the last 20 years has become more popular with electric utility applications in network cables, substation underground feeder cables, and distribution cables because of its long-term reliability and strong performance over a 50-year period. Generally, EPR insulations retain their break-down (dielectric) strength in service over the life of the installation, given proper storage and handling of the cable prior to installation of the cable. The superior flexibility of the EPR-insulated medium voltage cable is an important factor in larger (kcmil-sizes) as those cables must be trained and coiled in vaults and other enclosures. The linemen expend less effort, reducing risk of muscle strains. This insulation has a solid history of reliability, superior flexibility, and strong performance in wet applications, as well as improved flame retardancy over TR-XLP insulations. EPR compounds are rated 105ºC for normal operation, 140ºC for emergency operation and 250ºC short circuit.
Losses
The modern electrical distribution system has many contributors to electrical losses such as transformers, service conductors, arresters, secondary conductors and primary conductors. Dielectric losses occur in both TR-XLP and EPR compounds and it is well documented that EPR has significantly higher losses than TRXLP insulation. Decisions on the insulation type to be used should not be based on a single attribute.
Additional Improvements to Cable Design
Other key developments that improved cable life have been the use of strand-fill, where a conductive elastomer (rubber) is pumped within the wires of the conductor, minimizing the effect of water at the most critical point between the conductor and the conductor shield. Another significant development was the almost universal adoption of Linear Low Density Polyethylene (LLDPE) encapsulating jackets, which surround the concentric neutrals, providing another barrier to water, but more importantly adding another layer of tough, physical protection to guard against handling and installation damage prior to installation by the utility.
Regardless of the insulation type specified on medium voltage cable; proper handling, storage, correctly-sized accessories, proper stripping tools, and safe work practices ensure a successful installation and help promote a long service life of the installation. We also encourage the use of solid conductors, strand-fill in stranded wire and the use of LLDPE encapsulating jackets to ensure maximum cable performance.
Medium Voltage Cable Specifications
The specifications that govern the manufacturing of medium voltage underground cables are AEIC CS8-13 and the latest versions of ANSI/ICEA S-94-649 “Standard for Concentric Neutral Cables Rate 5 through 46kV” and S-97-682 “Standard for Utility Shielded Power Cables Rated 5 Through 46kV.”
These standards emphasize performance-based requirements for the materials used in manufacture of cable and for the finished product. These specifications are applicable to TR-XLP (tree-retardant cross-linked polyethylene) and EPR (ethylene propylene rubber) and do notendorse one insulation compound over another.
Note: Contribution: Ed Tafoya, SW/SC Regional Sales Manager – Utility, for Border States Electric, shared some of his cable expertise in the creation of this article.
Cross-linked polyethylene (XLP) compound was invented during the 1950s and gained popularity during the 1960s because it provided physical protection and flexibility, making it a staple in providing improved reliability in the electrical system. Cross-linked insulation was also affordable and could be mass produced by many suppliers. Therefore, it was the right compound at the right time.
In the early 1970s there were growing concerns that cable failure was linked to the ingress of moisture and contaminants into the cable core. Over time, this caused stress points within the insulation that led to the “treeing” phenomena. Treeing, over time, erodes the insulation, leading to cable failure.
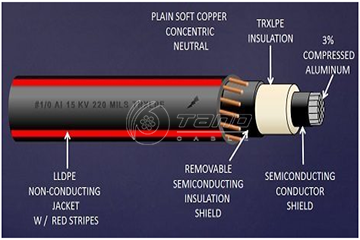
Since the mid-1980s, TR-XLP has become the dominant insulation in utility distribution cable applications primarily due to lower first-cost and lower operating losses. TR-XLP compound continues to be improved and is provided by many cable manufacturers in the United States and the rest of the world.
TRXLPE compounds are rated 90ºC for normal operation, 130ºC for emergency operation and 250ºC short circuit.
EPR
The first versions of EPR (ethylene propylene rubber-insulated), introduced in the early 1960s, demonstrated favorable characteristics that were quickly recognized by cable manufacturers. It presented weathering stability, heat resistance up to 160ºC, low temperature flexibility, and it was easily extruded.
Over the years, EPR insulation has become the standard insulation for most industrial applications, and in the last 20 years has become more popular with electric utility applications in network cables, substation underground feeder cables, and distribution cables because of its long-term reliability and strong performance over a 50-year period. Generally, EPR insulations retain their break-down (dielectric) strength in service over the life of the installation, given proper storage and handling of the cable prior to installation of the cable. The superior flexibility of the EPR-insulated medium voltage cable is an important factor in larger (kcmil-sizes) as those cables must be trained and coiled in vaults and other enclosures. The linemen expend less effort, reducing risk of muscle strains. This insulation has a solid history of reliability, superior flexibility, and strong performance in wet applications, as well as improved flame retardancy over TR-XLP insulations. EPR compounds are rated 105ºC for normal operation, 140ºC for emergency operation and 250ºC short circuit.
Losses
The modern electrical distribution system has many contributors to electrical losses such as transformers, service conductors, arresters, secondary conductors and primary conductors. Dielectric losses occur in both TR-XLP and EPR compounds and it is well documented that EPR has significantly higher losses than TRXLP insulation. Decisions on the insulation type to be used should not be based on a single attribute.
Additional Improvements to Cable Design
Other key developments that improved cable life have been the use of strand-fill, where a conductive elastomer (rubber) is pumped within the wires of the conductor, minimizing the effect of water at the most critical point between the conductor and the conductor shield. Another significant development was the almost universal adoption of Linear Low Density Polyethylene (LLDPE) encapsulating jackets, which surround the concentric neutrals, providing another barrier to water, but more importantly adding another layer of tough, physical protection to guard against handling and installation damage prior to installation by the utility.
Regardless of the insulation type specified on medium voltage cable; proper handling, storage, correctly-sized accessories, proper stripping tools, and safe work practices ensure a successful installation and help promote a long service life of the installation. We also encourage the use of solid conductors, strand-fill in stranded wire and the use of LLDPE encapsulating jackets to ensure maximum cable performance.
Medium Voltage Cable Specifications
The specifications that govern the manufacturing of medium voltage underground cables are AEIC CS8-13 and the latest versions of ANSI/ICEA S-94-649 “Standard for Concentric Neutral Cables Rate 5 through 46kV” and S-97-682 “Standard for Utility Shielded Power Cables Rated 5 Through 46kV.”
These standards emphasize performance-based requirements for the materials used in manufacture of cable and for the finished product. These specifications are applicable to TR-XLP (tree-retardant cross-linked polyethylene) and EPR (ethylene propylene rubber) and do notendorse one insulation compound over another.
Note: Contribution: Ed Tafoya, SW/SC Regional Sales Manager – Utility, for Border States Electric, shared some of his cable expertise in the creation of this article.
Previous article: