11
Oct
Differences between welding cables with pure copper wire conductors and welding cables with copper-clad aluminum conductors
Share:
Welding cables with pure copper wire conductors and welding cables with copper-clad aluminum conductors differ in terms of their construction, electrical properties, performance, and suitability for specific applications. Here are the key differences between the two:
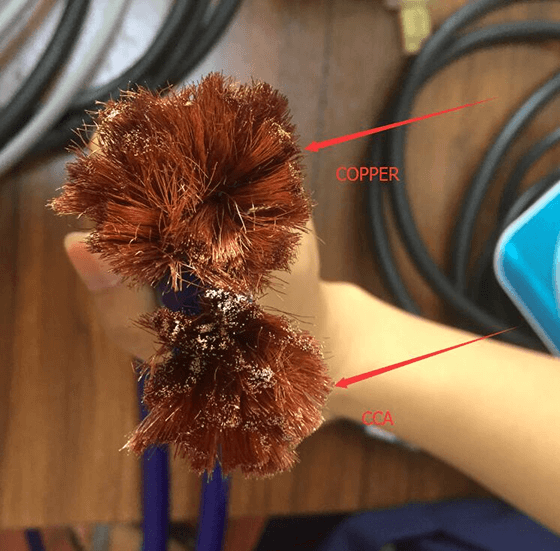
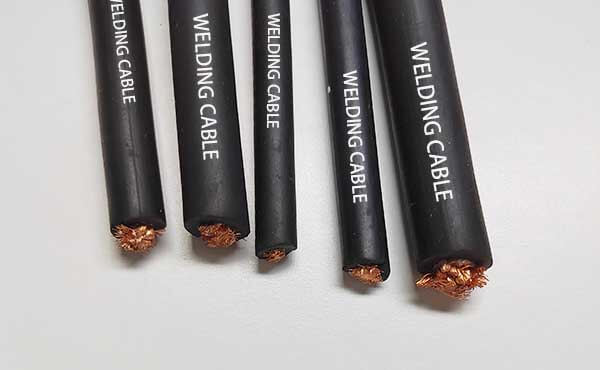
Consist of solid copper wire throughout the conductor.
Copper provides excellent electrical conductivity and heat resistance.
Typically more expensive compared to copper-clad aluminum conductors.
Comprise an aluminum core with a thin layer of copper coating (cladding) on the outside.Aluminum core offers lightweight properties, while the copper cladding provides superior conductivity.Generally more cost-effective compared to pure copper wire conductors.
2.1Conductivity:
Exhibits higher electrical conductivity compared to copper-clad aluminum.
Offers lower resistance, resulting in efficient current transfer.
Ideal for applications where high conductivity is crucial.
Possess lower electrical conductivity compared to pure copper wire conductors.Higher resistance compared to pure copper wire conductors, resulting in slightly reduced electrical efficiency.Suitable for applications where a balance between conductivity and cost-effectiveness is required.
2.2Resistance and Heat Dissipation:
Provide lower resistance, resulting in reduced heat generation during welding.
Excellent heat dissipation properties, allowing for efficient cooling.Preferred for high-power welding applications that require minimal heat buildup.
Inherently higher resistance compared to pure copper wire conductors, leading to relatively more heat generation during welding.Slightly reduced heat dissipation capabilities compared to pure copper wire conductors.Suitable for low to medium-power welding applications where heat management is not a critical concern.
3.1Current Carrying Capacity:
Higher current-carrying capacity, making them suitable for applications requiring high welding currents.Recommended for heavy-duty and industrial welding operations.
Lower current-carrying capacity compared to pure copper wire conductors.
Suitable for light to moderate welding applications that do not demand high current levels.
Superior mechanical strength and durability.
More resistant to breakage, bending, and other physical stresses.
Suitable for harsh operating conditions and frequent handling.
Relatively lower mechanical strength compared to pure copper wire conductors.Require careful handling to prevent breakage or damage.
Recommended for applications with minimal physical stress or movement.
It is essential to consider these differences and match the welding cables type to the specific requirements of the welding application. Factors such as power requirements, budget constraints, and the intended use will influence the selection between pure copper wire conductors and copper-clad aluminum conductors.
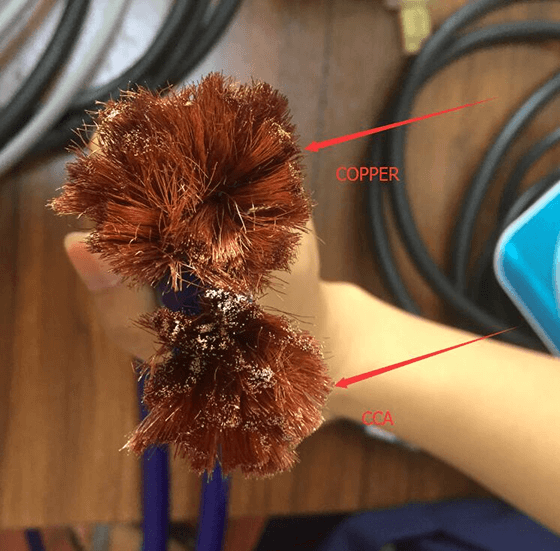
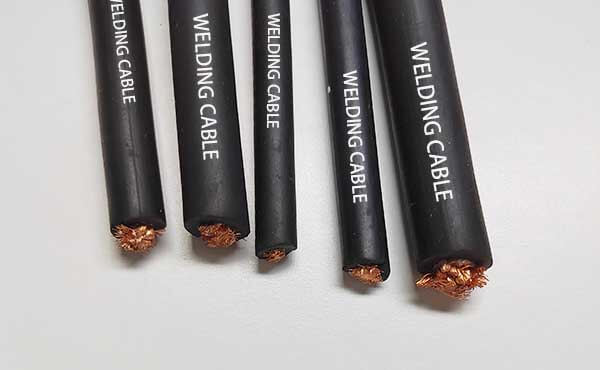
1 Construction and Materials:
Pure Copper Wire Conductors:
Consist of solid copper wire throughout the conductor.
Copper provides excellent electrical conductivity and heat resistance.
Typically more expensive compared to copper-clad aluminum conductors.
Copper-Clad Aluminum Conductors:
Comprise an aluminum core with a thin layer of copper coating (cladding) on the outside.Aluminum core offers lightweight properties, while the copper cladding provides superior conductivity.Generally more cost-effective compared to pure copper wire conductors.
2 Electrical Properties:
2.1Conductivity:
Pure Copper Wire Conductors:
Exhibits higher electrical conductivity compared to copper-clad aluminum.
Offers lower resistance, resulting in efficient current transfer.
Ideal for applications where high conductivity is crucial.
Copper-Clad Aluminum Conductors:
Possess lower electrical conductivity compared to pure copper wire conductors.Higher resistance compared to pure copper wire conductors, resulting in slightly reduced electrical efficiency.Suitable for applications where a balance between conductivity and cost-effectiveness is required.
2.2Resistance and Heat Dissipation:
Pure Copper Wire Conductors:
Provide lower resistance, resulting in reduced heat generation during welding.
Excellent heat dissipation properties, allowing for efficient cooling.Preferred for high-power welding applications that require minimal heat buildup.
Copper-Clad Aluminum Conductors:
Inherently higher resistance compared to pure copper wire conductors, leading to relatively more heat generation during welding.Slightly reduced heat dissipation capabilities compared to pure copper wire conductors.Suitable for low to medium-power welding applications where heat management is not a critical concern.
3 Performance and Application Considerations:
3.1Current Carrying Capacity:
Pure Copper Wire Conductors:
Higher current-carrying capacity, making them suitable for applications requiring high welding currents.Recommended for heavy-duty and industrial welding operations.
Copper-Clad Aluminum Conductors:
Lower current-carrying capacity compared to pure copper wire conductors.
Suitable for light to moderate welding applications that do not demand high current levels.
3.2Mechanical Strength and Durability:
Pure Copper Wire Conductors:
Superior mechanical strength and durability.
More resistant to breakage, bending, and other physical stresses.
Suitable for harsh operating conditions and frequent handling.
Copper-Clad Aluminum Conductors:
Relatively lower mechanical strength compared to pure copper wire conductors.Require careful handling to prevent breakage or damage.
Recommended for applications with minimal physical stress or movement.
Summary
It is essential to consider these differences and match the welding cables type to the specific requirements of the welding application. Factors such as power requirements, budget constraints, and the intended use will influence the selection between pure copper wire conductors and copper-clad aluminum conductors.